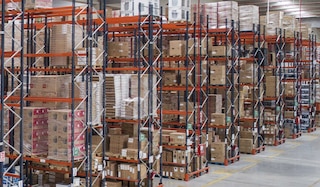
Los 10 problemas logísticos más comunes en un almacén
La continua evolución hacia los mercados digitales y las nuevas exigencias de los clientes ha acarreado un notable aumento de los problemas logísticos, especialmente de aquellos relacionados con la gestión del almacén.
Pero, ¿cuáles son los problemas logísticos más comunes? Identificamos los diez más habituales que se dan en un almacén y sugerimos algunas soluciones para minimizar sus consecuencias.
1. Espacio desaprovechado
La falta de espacio de almacenaje es uno de los principales problemas con el que se encuentran la mayoría de empresas. Ante esta situación, provocada mayoritariamente por un incremento de la actividad, las compañías tienen la obligación de optimizar el espacio si no quieren hacer un considerable desembolso económico en suelo logístico.
Una de las soluciones más recurrentes para maximizar el espacio sin alterar la superficie es aprovechar la altura del almacén mediante la utilización de estanterías de mayor altura o entreplantas y pasarelas. También podemos optimizar la superficie con la instalación de sistemas de almacenamiento compacto, como el Pallet Shuttle, estanterías móviles Movirack o estanterías compactas drive-in.
2. Falta de organización de la mercancía
La falta de organización de la mercancía ocasiona errores y demoras a la hora de buscar un determinado producto, dificultando el cumplimiento de los tiempos de entrega. Un almacén ordenado es el primer paso hacia la eficiencia logística.
Para evitarlo, es preciso elaborar una eficiente estrategia de ubicación de la mercancía que tenga en cuenta las características de las referencias, los sistemas de almacenaje disponibles, la rotación de la mercancía y los desplazamientos de los operarios.
Hacer uso de un sistema de gestión de almacenes garantiza el control íntegro del stock que hay en el almacén, al sincronizar las órdenes de entrada y salida. Un SGA, por ejemplo, automatiza el proceso de ubicación de las referencias en el almacén (slotting) mediante criterios y reglas previamente configuradas.
3. Errores en el picking
Desde coger el artículo erróneo hasta mezclar varios pedidos en una sola orden, el costo de la logística inversa ─la devolución de artículos─, causada por fallas en el picking, tiene graves consecuencias en la logística de una empresa.
Los errores en el picking suponen un alto costo para el negocio. Según ciertos estudios, su impacto promedio se estima en unos 17€ por pedido.
En una operativa tan compleja como la preparación de pedidos, donde usualmente los operarios elaboran múltiples pedidos de distintas referencias, automatizar es la solución para suprimir la tasa de error y aumentar el número de picks por hora que se completan en el almacén.
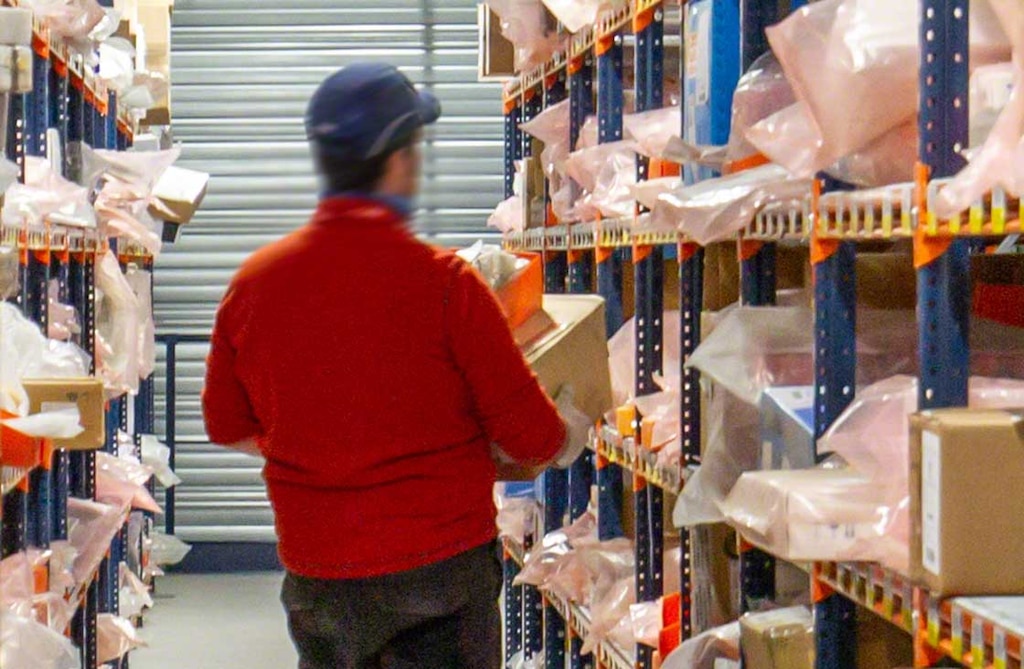
4. Falta de trazabilidad
En un contexto de cadena de suministro integrada, clientes y proveedores demandan conocer al detalle de qué materias primas está elaborado un artículo y cuáles son los procesos productivos y logísticos por los que ha pasado hasta llegar a sus manos.
La trazabilidad del producto, el atributo logístico que permite registrar e identificar cada producto desde su origen hasta su destino final, es especialmente delicada en sectores como el farmacéutico o el agroalimentario. Un error de trazabilidad puede acarrear graves problemas para los clientes que adquieran el producto, así como para la empresa proveedora.
La implementación de un software logístico como un SGA garantiza la trazabilidad del producto desde su entrada en el almacén hasta su expedición. Además de esta aplicación, existen otros software en el mercado que potencian este atributo logístico como, por ejemplo, la funcionalidad avanzada de Easy WMS, SGA para producción. Este módulo sincroniza el pulmón de abastecimiento con el de producción a fin de monitorizar el proceso de producción en un almacén.
5. Inventario desactualizado
Conocer y planificar el stock de un almacén es indispensable para mantener la productividad en todas las operaciones logísticas. No en vano, un almacén con un inventario desactualizado puede implicar graves consecuencias para una empresa, desde errores en la ubicación de productos hasta una posible rotura de stock.
A medida que las empresas crecen e incorporan más referencias en su almacén, la implantación de un sistema de gestión de almacenes se convierte en una herramienta necesaria para conocer en todo momento el stock disponible del almacén.
6. Errores en la manipulación de la mercancía
Manipular correctamente las unidades de carga para conformar los pedidos es una de las claves para reducir errores y aumentar la productividad. Hay que asegurarse de que los operarios estén convenientemente formados, que el almacén disponga de los equipos de manutención adecuados y que estos cuenten con el mantenimiento necesario.
Sin embargo, la opción que mejor garantiza la manipulación idónea de la mercancía es la automatización de los sistemas de almacenaje. Los responsables de logística optan por sustituir los equipos de manutención convencionales, como estibador y montacargas contrapesados, por transportadores y transelevadores, con el objetivo de agilizar el tránsito de la mercancía entre los diferentes procesos logísticos.
Además, al manipular la mercancía, es importante garantizar la estabilidad de las unidades de carga, usualmente estibas o cajas, para asegurar la estabilidad del bulto a lo largo de todas las operativas que se realizan en el almacén.
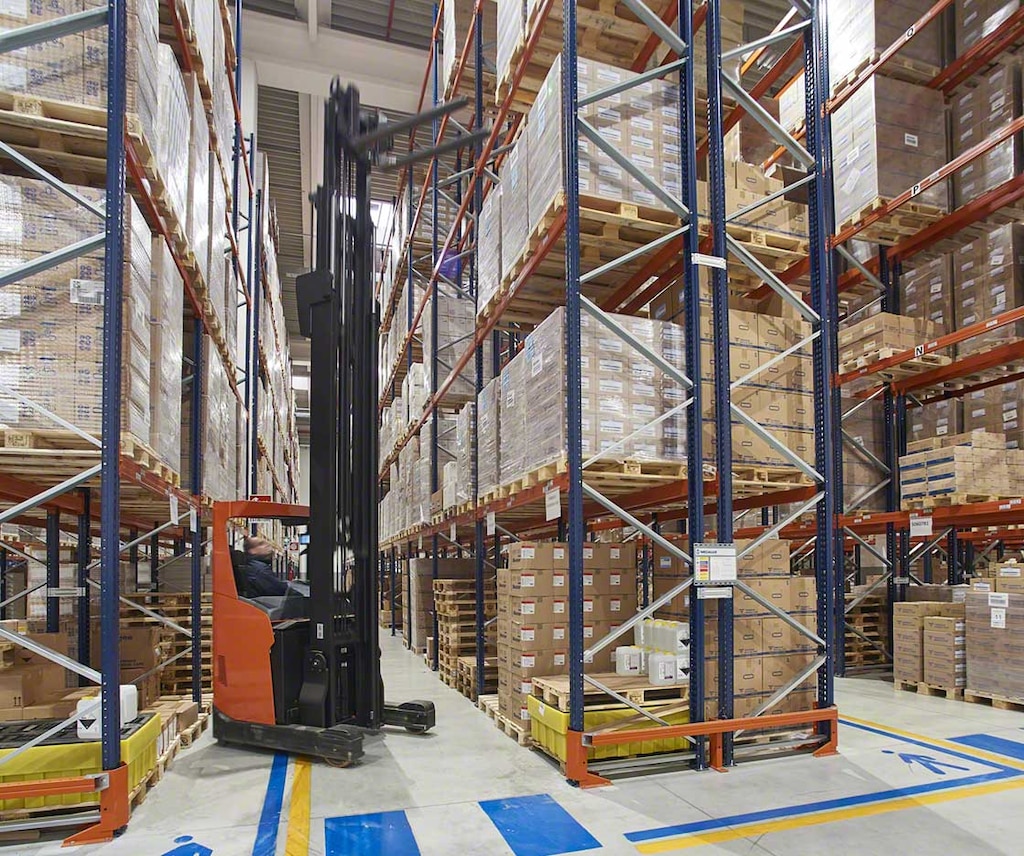
7. Demoras en las expediciones
La expedición de la mercancía es el último proceso por el que discurre un producto antes de ser expedido, bien al cliente final, bien a otro centro de distribución o producción.
Para que este proceso sea completado con éxito, es recomendable contar con una planificación de las entregas a realizar, una consolidación de la mercancía eficiente, una correcta comprobación de toda la documentación necesaria para la expedición y una rápida y segura carga de la mercancía en el camión.
Un sistema de gestión de almacenes es capaz de agrupar los pedidos por ruta de reparto, tipo de vehículo, cliente o prioridad del envío, entre otros.
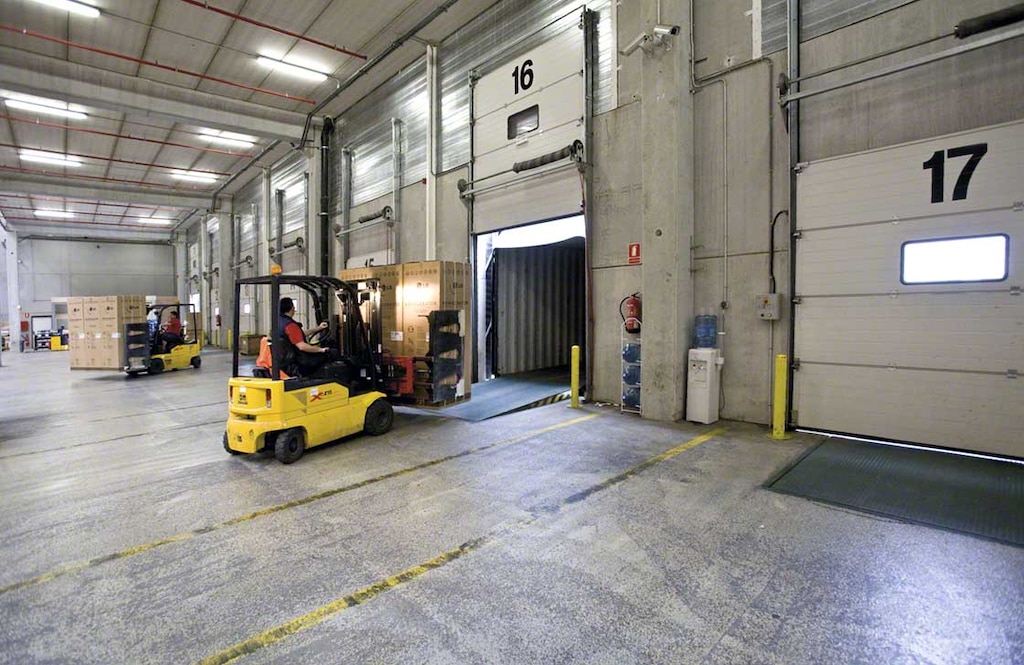
8. Señalización deficiente del almacén
En un espacio en el que cohabitan operarios, mercancía y equipos de manutención, es obligatorio disponer de una señalización del almacén que minimice los riesgos de accidente. Las señales deben estar perfectamente ubicadas y visualmente diferenciadas en el suelo y en las estanterías para que cumplan las medidas de seguridad.
La norma que obliga y regula la señalización del almacén está sujeta a la Directiva 92/58/CEE del Consejo Europeo, la cual define cómo deben ser las señales en un almacén. Dichas señales pueden ser de distintos colores, símbolos y formas dependiendo de sus características y del mensaje que deban transmitir.
9. KPI logísticos incorrectos
La mejor herramienta para llevar a cabo acciones de mejora continua en nuestro almacén es mediante indicadores de rendimiento o KPI logísticos (Key Performance Indicators). A través de los datos y la comparación con el histórico de la empresa, podemos monitorizar el rendimiento de una operativa para encontrar oportunidades de mejora.
Los KPI logísticos permiten medir todas las operaciones que se efectúan en un almacén: recepción de mercancías, almacenaje, preparación de pedidos, gestión de inventarios, expediciones, entregas, transporte y gestión de devoluciones, entre otras. Si no utilizamos correctamente estos indicadores o centramos nuestros esfuerzos en analizar KPI incorrectos, nos costará muchísimo identificar evoluciones positivas o negativas y actuar en consecuencia a fin de alcanzar la excelencia logística.
Un módulo como Supply Chain Analytics Software monitoriza toda la actividad que se produce en el almacén, calculando los KPI logísticos más relevantes para su posterior análisis.
10. Integración con otros departamentos (ERP)
El jefe de almacén ha de estar coordinado con los demás departamentos de la empresa para conseguir el objetivo final de toda logística: que el pedido llegue en el tiempo y de la forma acordada con el cliente.
Con ese fin, los diferentes software logísticos se integran dentro del ERP (Enterprise Resourcing Planning), un programa informático que agrupa todas o la mayoría de divisiones de una compañía como, por ejemplo, contabilidad, marketing, departamento comercial, etc.
Una mala coordinación entre el almacén y la división de ventas puede ocasionar que haya errores en los pedidos o pedidos incompletos, lo que supone graves consecuencias económicas para la compañía.
Benefíciate de un almacén más eficiente
En líneas generales, la automatización, tanto de la operativa como de la gestión de un almacén mediante un SGA, es la mejor estrategia para un almacén libre de errores y mucho más eficiente.
Si tu almacén padece alguno de los problemas mencionados anteriormente o crees que ha llegado la hora de robotizar tanto el almacenaje como la gestión de tu centro de distribución, no dudes en contactar con Mecalux. Un equipo de expertos te ayudará a solucionar cualquier contratiempo a fin de sacar el máximo rendimiento a tus procesos logísticos.