Robots colaborativos y robots industriales: ¿por qué apostar por ellos en el almacén?
Los robots colaborativos y los robots industriales son dos de las puntas de lanza de la automatización logística. Estas máquinas agilizan todas las operativas de un almacén y, sobre todo, eliminan el riesgo de cometer errores derivados de la manipulación manual de los productos.
En este artículo nos adentramos en las principales diferencias entre robots colaborativos e industriales y analizamos las claves para escoger entre unas máquinas u otras.
Robótica en la logística 4.0
Los robots comenzaron a emplearse en logística hace más de 40 años, sobre todo en industrias con complejos procesos productivos y que requerían mover grandes volúmenes de carga. Sin embargo, la logística 4.0 ha impulsado avances tecnológicos como el internet de las cosas industrial (IIoT) o el machine learning, que han posibilitado sustituir a grandes robots pesados por otro tipo de máquinas capaces de optimizar procesos por sí mismas.
Gracias a estas tecnologías, cada vez son más las instalaciones que apuestan por automatizar los procesos en el almacén. Según un estudio de la consultora ABI Research, hacia 2025 se habrán instalado más de 4 millones de robots en 50.000 almacenes en todo el mundo.
En un escenario de incremento de la competencia, las compañías se han visto obligadas a reemplazar el trabajo manual por máquinas que automaticen las tareas más repetitivas o pesadas. La introducción de la robótica se ha popularizado en procesos logísticos como la recepción y ubicación de mercancía ―con sistemas automatizados como el Pallet Shuttle automático o los transelevadores para estibas―, el movimiento de cargas ―con los transportadores para cajas― o la expedición de pedidos, con sórteres (sistemas de clasificación automática) que permiten expedir los productos según su ruta de reparto.
La utilización de robots en un almacén posibilita:
- Eliminar el riesgo de errores derivados de la gestión manual de mercancía.
- Acelerar el flujo de mercancías y los movimientos de cargas.
- Disponer de un mayor control sobre el stock.
- Ahorrar espacio de almacenaje al compactar la mercancía.
- Garantizar la máxima seguridad para la mercancía, los operarios y la instalación.
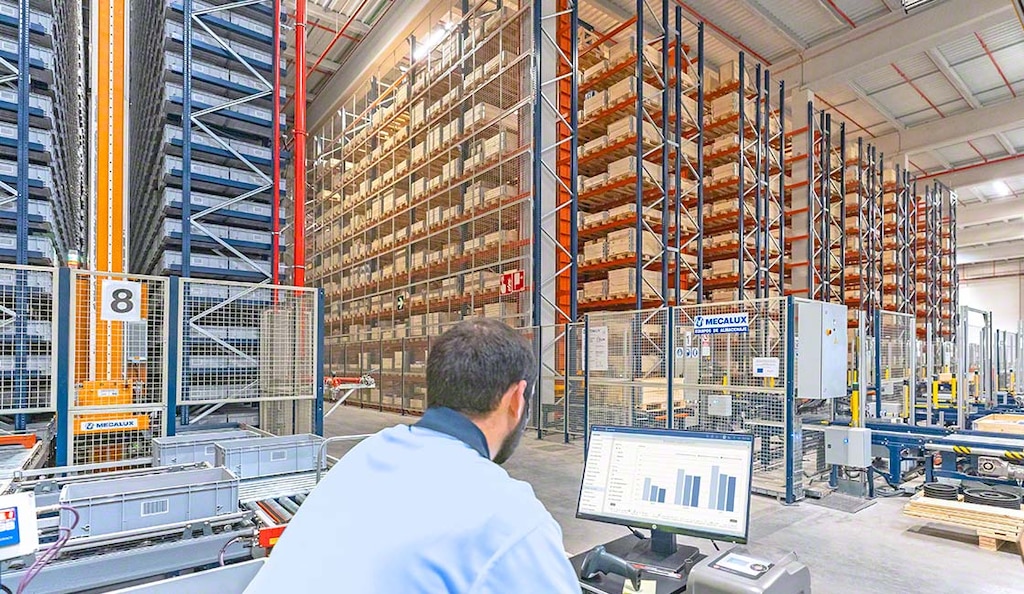
¿Qué es un robot colaborativo?
Los robots colaborativos o cobots son máquinas diseñadas para trabajar junto a los operarios en una cadena de producción o un almacén. Su diseño asegura que el operario pueda establecer un contacto seguro con la máquina, garantizando tanto su protección como la de la mercancía. Estándares internacionales como la ISO 10218-1 o la ISO/TS 15066 se encargan de establecer las pautas de seguridad necesarias para el trabajo conjunto de máquinas y operarios.
Aunque la cobótica se halla muy presente en sectores que requieren fuertes procesos de fabricación, como la industria automotriz, es una solución cada vez más habitual en todo tipo de empresas. De hecho, los robots colaborativos se emplean en cualquier operación logística o de producción que implique movimientos de cargas que pueden resultar excesivas para que las manipule un operario.
En lugar de sustituir al operario, este tipo de maquinaria se implanta en los almacenes y centros de producción para complementar sus tareas y optimizar su rendimiento. Por ejemplo, los robots colaborativos desempeñan aquellas acciones que suponen un mayor desgaste para los operarios, como el embalaje de pedidos o el pick and place de artículos pesados. Entre los mejores ejemplos de cobótica en logística, encontramos los brazos robóticos que se ubican en las estaciones de picking y que agilizan la preparación de pedidos o, también, los cobots, que complementan al operario a la hora de paletizar o empaquetar un producto.
¿Qué es un robot industrial?
Un robot industrial es una máquina de manipulación de mercancía programable que se coloca en un almacén o centro de producción para ejercer tareas muy especializadas como la ubicación y extracción de stock o el movimiento de grandes volúmenes de carga. Su principal función es reemplazar las tareas manuales con un único fin: aumentar la productividad, compactar la mercancía y suprimir el riesgo de error. Estos equipos destacan por su gran capacidad para operar masivamente con mercancía (24 horas, 7 días a la semana) sin que un operario intervenga.
Ese es el caso de los transelevadores para cajas. Estos sistemas de almacenaje automáticos se sitúan entre dos pasillos de estanterías, dinamizando la extracción y depósito de cajas y bandejas en el almacén sin necesidad de intervención humana. El transelevador recoge la mercancía y la emplaza en aquella ubicación que le indica el sistema de gestión de bodegas, el cual, a su vez, programa todos los movimientos que ejecuta la máquina. Lo mismo ocurre durante el proceso de extracción: el transelevador o miniload toma la caja que le señala el programa de gestión y la coloca en los transportadores, que la conducen al puesto de picking.
Otro ejemplo es el de los transportadores para estibas y los transportadores para cajas. Con ellos pueden crearse circuitos predeterminados que aceleran el flujo de mercancías entre distintas zonas del almacén o entre estaciones contiguas.
Razones para escoger robots colaborativos o robots industriales
La robótica asegura una mayor eficiencia en los procesos de un almacén. Pero, ¿por qué optar por robots colaborativos e industriales ? La planificación logística, las operativas y el layout del almacén determinarán si los procesos manuales han de ser sustituidos por cobots o por sistemas automáticos como transelevadores o transportadores.
La primera gran distinción entre estos dos tipos de robots es su grado de especialidad: los robots industriales acostumbran a emplearse en solo una tarea, ocupan mucho espacio y cuentan con un recorrido fijo, mientras que los cobots son una solución flexible que puede reubicarse en diferentes áreas del almacén según las necesidades logísticas. Por su parte, el robot industrial es también una herramienta ideal para agilizar tareas que impliquen alta densidad de trabajo y repetición constante de movimientos, como es el caso de la extracción y ubicación de productos.
Por estos motivos, cada responsable logístico debe valorar si requiere de un tipo de maquinaria u otra en función de las demandas existentes. Una instalación que precise mover dinámicamente elevadas cantidades de producto puede remplazar los montacargas elevadores por un sistema de transporte automático como transportadores o electrovías, siempre y cuando los flujos de mercancías sean repetitivos. A diferencia de los robots colaborativos, estas máquinas no emplean el machine learning para ejercer sus funciones, sino que operan a partir de algoritmos avanzados para completar los recorridos que les asigna el sistema de gestión de almacenes.
Automatización de procesos: eficiencia y productividad para el almacén
Hoy en día, las compañías incorporan soluciones robóticas para ganar en eficiencia y productividad. Tanto los robots colaborativos como los industriales han sido desarrollados para agilizar los movimientos en el almacén y optimizar la productividad.
Si estás interesado en incrementar la competitividad de tus operativas logísticas, no dudes en contactar con nosotros. Un consultor experto valorará tu situación y te asesorará en la mejor solución para tu empresa.